Elevating Healthcare Environments with Stonhard's Advanced Flooring Systems
Application area: Operating Room
Ontario Tech University (formerly UOIT) operates a world class climatic wind tunnel used for product development, proof of concept and R&D at the Automotive Centre of Excellence (ACE) facility on the Oshawa Campus. This can be used to re-create any weather condition a test object might experience, from the blistering heat of Death Valley to the frigid conditions found in the Arctic (-40ºC to +60ºC) and can simultaneously test vehicles operating under full load with crosswinds and wind speeds up to 280 km/h.
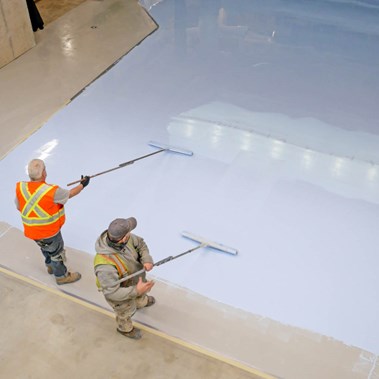
As part of an expanded program, Ontario Tech University were adding a Moving Ground Plate (MGP) to supplement the Dynamometer currently in operation. Both pieces of equipment are extremely large and are moved on air bearings, allowing them to be switched into the test location under the climatic chamber prior to raising them into place.
The Dynamometer is approximately 250,000 lbs and the MGP is 150,000 lbs. Once the MGP is operational, it is anticipated that the two pieces of equipment will be swapped in and out of the climatic chamber at least three times per month.

THE CHALLENGE
The MGP required the basement floor to be extremely flat and level to ensure the accuracy of measurements taken. Following 10 years of large climatic swings combined with the constant weight of the Dynamometer, the basement floor did not meet the flatness or levelness tolerances required for this new high precision equipment. Stonhard was tasked with providing a floor solution that would be both flat and level, and able to resist the imposed loads during regular equipment movements on air jacks and once landed during operation, while being subjected to a temperature swings of 0ºC to +40ºC with water spilling onto the surface as the climatic chamber above is in operation. Ontario Tech University provided a floor survey of the critical area under the test chamber where the equipment landed that showed as much as 22 mm total deviation in this critical location. The floor was to be installed during a small shutdown in operations coinciding with the build up of the new MGP, allowing limited access for heavy equipment. Our preparation equipment and materials were craned into the basement area prior to the project starting. The limited shutdown and access window meant that the project would be installed as a continuous process that included weekend work to meet the deadline for restarting operations with the Dynamometer.
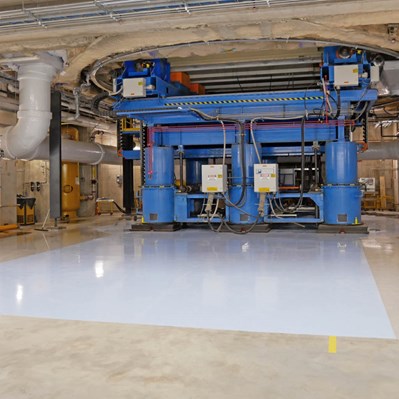
THE STONHARD SOLUTION
Stonhard used a combination of precision surveying, grinding and levelling with Epoxy Mortars to identify and help eliminate high points and hollows, allowing us to precisely flatten and level the floor to meet the target tolerances of FF & FL 50 (less than 3 mm of deviation) required for the MGP, prior to installing a final low friction wearing surface of Stonlux SL in the critical equipment travel path and landing areas below the climatic chamber. Stonlux SL is a tough, ultra smooth, liquid rich, chemical and impact-resistant self-leveling flooring system, making it an ideal choice for environments that require durable low-friction floors.